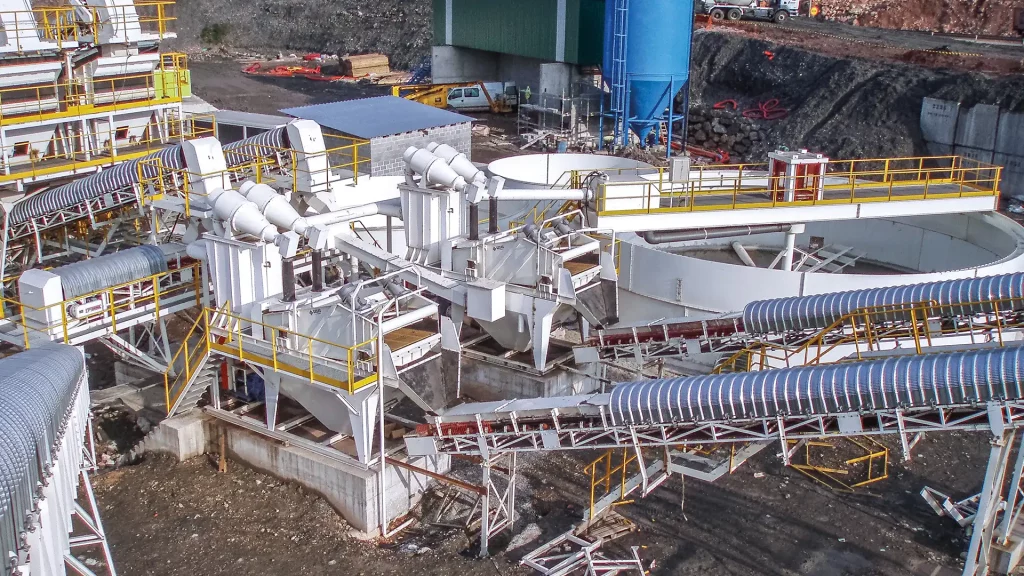
Sand Washing Plants
MOGENSEN sand washing plants play a critical role in the industry by producing high-quality sand for a wide range of applications. These plants are specifically designed to process sand that meets the stringent industrial requirements for grain size distribution, fineness modulus, cleanliness, and consistency. Additionally, they effectively reduce the content of undesirable elements such as organic matter, chlorides, and sulfates. MOGENSEN sand washing plants are utilized in various industries, including concrete production, frac sand, foundry sand, and other industrial sand processing. They are also essential for processing bentonite slurries and other minerals. By using modern MOGENSEN sand washing plants, the highest sand quality is achieved, which is particularly crucial for specialized construction industry applications and other industrial processes. These plants enhance efficiency and sustainability by optimizing both sand quality and material usage.
Structure of a Sand Washing Plant
1. Material Collection and Feeding
- The material is collected and fed through a chute.
- A feeding system regulates the material flow into the subsequent processing steps.
2. Separation and Washing of Different Grain Sizes
- Separation takes place using a MOGENSEN screen with water spray (wet screening).
- Different grain sizes, such as gravel and other fractions, are collected beneath the screen.
- These materials are then transported either between walls or via conveyor belts for storage.
3. Washing and Dewatering of Sand and Wastewater
- Fine sand sludge and water passing through the smallest mesh of the screen undergo further processing.
- A hydrocyclone with a dewatering screen (sand washing unit) ensures the washing and dewatering of the sand.
- The results of this phase:
- Washed and dewatered sand
- Wastewater, still containing fine particles.
4. Transporting Clean Sand for Storage
- The cleaned sand is transported via a conveyor belt for storage.
- A swing stacker is often used to distribute the sand efficiently.
5. Clarification of Contaminated Water
- The water, containing clay and fillers, is purified in a settling tank or clarifier.
- A flocculation solution is used to bind and separate particles.
- Objectives of this step:
- Maximize water recovery for reuse in the process.
- Reduce sludge volume to optimize storage capacity or increase the efficiency of filter presses.
functionality
Efficient Sand Washing with Hydrocyclones
Using sand washing machines equipped with hydrocyclones is the most effective method for obtaining high-quality washed sand. This process efficiently removes particles in the 63–106 µm (250–140 mesh) range, outperforming traditional systems like water wheels or screw washers. The result is high-quality sand with a minimal amount of particles smaller than 75 µm, while fine sand is largely preserved.
Customizable Equipment for Optimal Performance
Each washing unit is equipped with tailor-made components, including:
- Pumps
- Motors
- Dewatering screens
- Hydrocyclones
These components are selected based on the specific requirements of each application. With a wide range of available combinations, we can design customized machines that optimize the investment into the production plant.
Multistage Washing for Maximum Purity
Depending on the desired product quality and the amount of fine particles to be removed, a multistage washing process may be required. In this process, the material discharged from the vortex of the first hydrocyclone is transferred to the tank of the next hydrocyclone. This cycle is repeated until the sand washing process is complete and the sand is fully cleaned.
product details
Challenges After the Washing Process and Their Solution
After the washing process, two key challenges arise:
- Managing the sludge generated during washing
- Recovering water for reuse
The ideal solution is to install a settling tank or clarifier combined with an efficient flocculation solution with automated dosing. This setup ensures effective separation of water and solids, reducing environmental impact while promoting sustainable water use.
Applications
MOGENSEN sand washing plants are essential for the processing of high-quality sand used across various industries. They are utilized in applications such as concrete production, frac sand, foundry sand, and the processing of other industrial sands. Additionally, they play a crucial role in the treatment of bentonite slurries and other minerals. Equipped with state-of-the-art technology, these plants ensure optimal sand quality, reduce unwanted components, and contribute to the efficiency and sustainability of industrial processes.
MOGENSEN sand washing plants ensure thorough cleaning and separation of sand.
Efficient processing and sorting of gravel.
Precise separation and cleaning of chalk materials.
Optimized processing and separation of basalt rock.
Reliable processing of limestone.
Sand Washing Plants
MOGENSEN sand washing plants are specially designed to produce high-quality sand for demanding industrial applications, effectively removing unwanted elements. They deliver the highest sand quality and are widely used in applications like concrete production, foundry sand, and industrial sand processing.
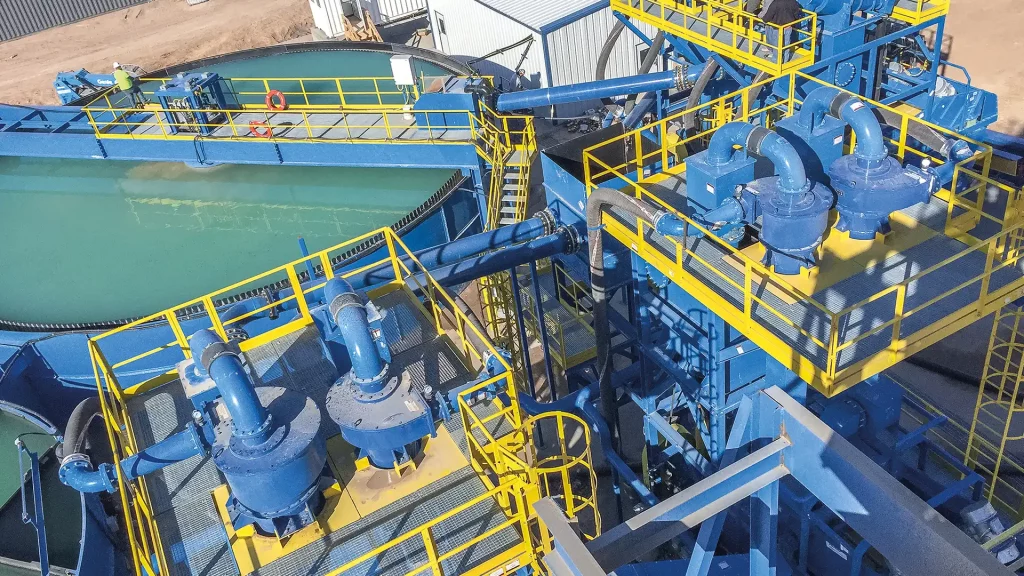
Clarification Units
The wastewater generated during the process, loaded with fines, is directed through a mixing box where it is combined with a flocculation solution. The dosing and concentration of the flocculant are critical for process optimization.
In the mixing box, the dirty water and flocculant are forced to follow a specific path to form flocs of the proper size and shape. After this phase, the mixture flows into a central pipe, where sludge quickly settles at the bottom.
The clarifier is equipped with a sludge pump that removes the sludge from the clarifier’s central cone and pumps it to the desired discharge point (standard maximum pumping capacity is 3 bar or 45 psi).
The pump automatically starts when the rake torque increases, indicating that the sludge has reached the ideal consistency and concentration. It stops when the concentration decreases.
To prevent sludge buildup due to debris, a rake lift system is installed, automatically controlled by the rake’s torque.
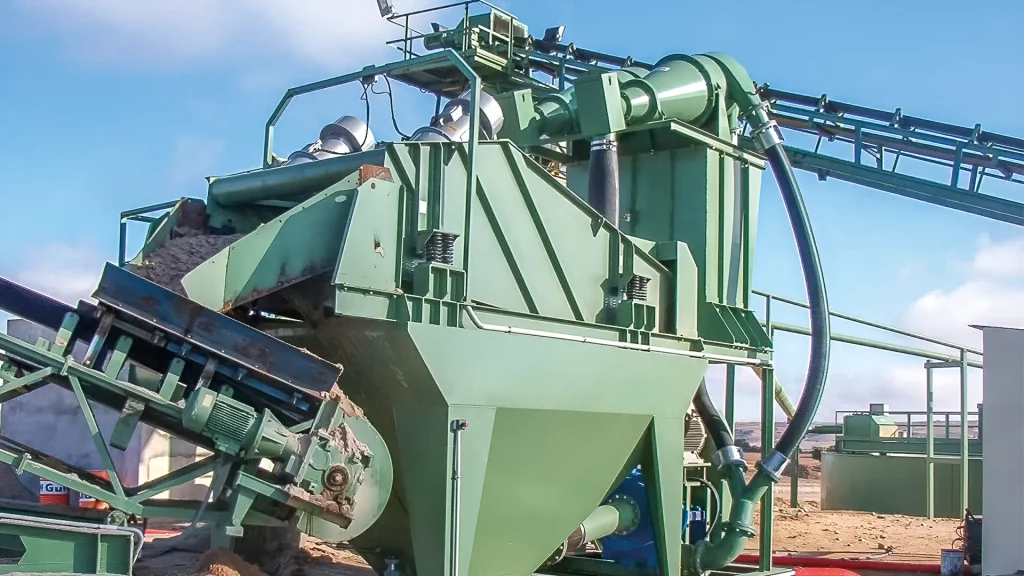
Flocculation Solution
As mentioned earlier, the proper preparation of the flocculant is fundamental for sludge treatment. Grit washers are equipped with an automatic control system to regulate each phase.
Different types of AUTOFLOC are available, depending on the material throughput in the range of 60–105 µm.
The flocculant is dosed via a pump, whose speed is adjusted by a frequency converter based on the contamination of the incoming material.
Proper control of the flocculation solution dosage reduces costs significantly. CONTROLFLOC automates this process without requiring dedicated personnel for monitoring.
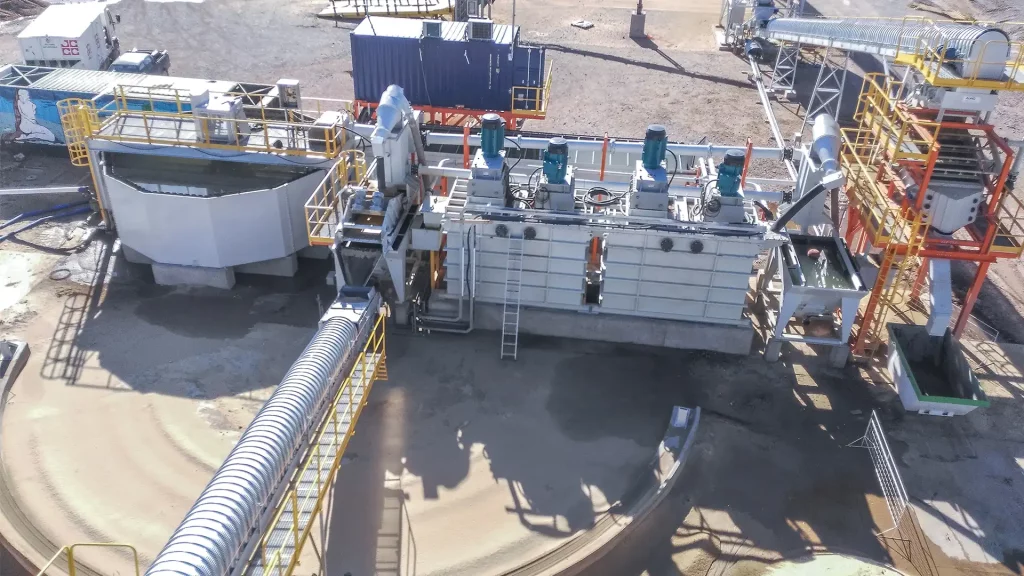
Desanding Units
MOGENSEN’s desanding units are primarily used for water reclamation with bentonite in drilling applications during foundation construction.
These units separate rock and sand debris, allowing bentonite to be reused along with water in foundation construction. They are also used in processes requiring hydrocyclone separation for finer particle sizes than those achieved by sand washing plants, such as cleaning concrete mixers or remediating contaminated soils.
Types of Bentonite Desanders
a) Single-Stage Hydrocyclones: Recommended for soils with low sand content or low fine sand concentration, with flow rates from 50 to 400 m³/h.
b) Two-Stage Hydrocyclones: Necessary for sandy soils, ensuring effective sand removal for any type of soil, with flow rates from 40 to 220 m³/h.
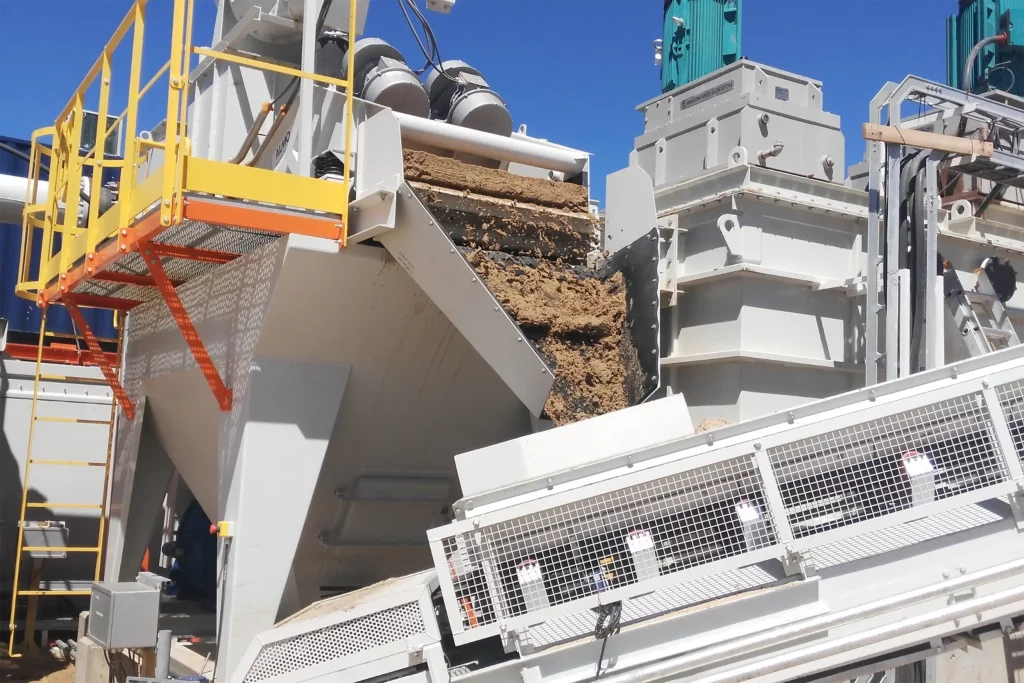
Other Applications of Hydrocyclones
The use of hydrocyclones in industrial applications has proven to be highly effective, particularly in the processing of quartz sand, feldspar, or kaolin clay.
This type of operation is more complex than simple sand washing, as it requires precise control over separation thresholds.
Depending on the desired separation limit and throughput capacity, the diameter and number of hydrocyclones should be carefully selected. In some cases, micro-cyclone arrangements and multiple hydrocyclone stages may be necessary to achieve the required separation efficiency.
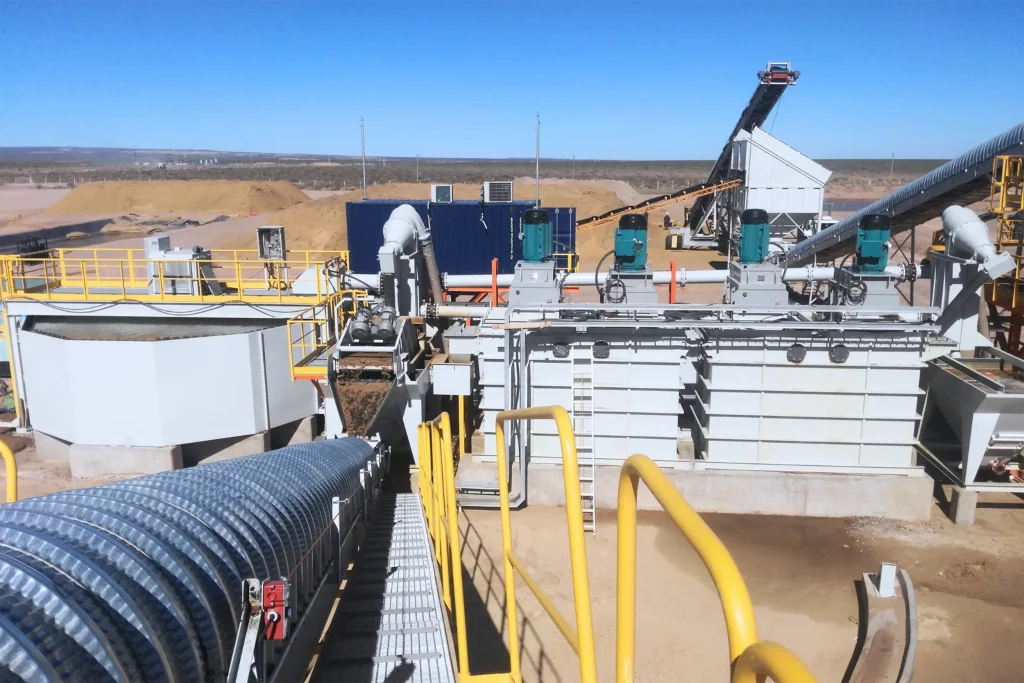
Dewatering Screens
Dewatering screens are typically used to remove excess water from materials discharged from washing equipment. They are also suitable for applications requiring concentrated slurry.
Vibration is generated by two motors, creating a linear motion that transports the dewatered product to the outlet. Water is filtered through high-quality polyurethane screens designed to prevent clogging.
Key Advantages
MOGENSEN sand washing plants stand for maximum efficiency and quality in processing sand and other materials. They remove unwanted elements such as chlorides and sulfates, ensuring high-quality sand that meets stringent industrial standards. Their adaptability and sustainability make them versatile and essential for optimizing production processes.
Configurable Systems
Adaptable to various materials and requirements.
Wide Applications
Suitable for everything from concrete production to industrial sand processing.
Sustainable Resource Use
Water treatment and material recovery ensure eco-friendly production.
High-Quality Sand
Consistently delivers top-quality sand.
Effective Element Removal
Reliably eliminates unwanted substances like chlorides and sulfates.
Test Your Material with Our Machines
At our MOGENSEN Test Center, experience firsthand how our proven Sand Washing Plants process your material with maximum precision and efficiency. Rely on state-of-the-art technology and trusted results. Contact our sales team to schedule an appointment and test your material under real conditions. We look forward to supporting you!
Get in touch with us
Reach out to us quickly and directly by using the contact form. We will respond as soon as possible!